Commercial asbestos removal extracts asbestos-containing materials from a building, using specialized skills and equipment to prevent fiber release. Asbestos encapsulation seals the material to stop fiber release, suitable when removal isn’t feasible.
Both methods ensure safe environments and compliance with Florida’s regulations. Commercial property owners must understand these processes to protect occupants and avoid legal issues.
What Is Commercial Asbestos Removal?
Commercial asbestos removal is the process of safely extracting asbestos-containing materials (ACMs) from business properties. It requires specialized equipment and trained professionals to minimize health risks.
Key aspects:
- Identification: Experts locate and assess ACMs in the building.
- Planning: A removal strategy is developed, adhering to safety regulations.
- Containment: Work areas are sealed to prevent asbestos fiber spread.
- Removal: ACMs are carefully extracted using approved techniques.
- Disposal: Removed materials are properly packaged and discarded at designated facilities.
- Clearance: The area is thoroughly cleaned and air-tested to ensure safety.
Professional removal is vital for:
- Protecting occupant health
- Complying with Florida regulations
- Maintaining property value
Removal costs and timeframes vary based on project scope.
What Are The Steps For Commercial Asbestos Removal?
The steps for commercial asbestos removal are:
- Inspection and Assessment
- Licensed inspectors examine the property
- Samples are collected and analyzed
- Extent of asbestos contamination is determined
- Planning and Preparation
- Detailed removal plan is created
- Required permits are obtained
- Occupants are notified and relocated if needed
- Site Setup
- Work area is sealed off
- Negative air pressure system is installed
- Decontamination units are set up
- Asbestos Removal
- Workers don protective gear
- ACMs are carefully removed using wet methods
- Materials are bagged and sealed
- Cleanup and Decontamination
- Work area is thoroughly cleaned
- HEPA vacuums and wet-wiping are used
- Equipment and workers are decontaminated
- Waste Disposal
- Sealed asbestos waste is transported to approved facilities
- Proper documentation is maintained
- Final Inspection and Air Testing
- Independent inspectors check the area
- Air samples are taken to ensure safety
- Clearance and Reoccupation
- Results are reviewed
- If cleared, area is reopened for use
Each step is crucial for safety and regulatory compliance. Proper execution by certified professionals ensures effective asbestos abatement.
What Is Commercial Asbestos Encapsulation?
Commercial asbestos encapsulation is a method used to manage materials containing asbestos in commercial buildings. This process involves applying a sealant to asbestos-containing materials, effectively locking them in place. The goal is to prevent asbestos fibers from becoming airborne and posing health risks.
When is encapsulation appropriate?
Encapsulation can be a suitable option in several scenarios:
- When the asbestos-containing material is in good condition
- If the material is unlikely to be disturbed or damaged
- In cases where removal would be too disruptive or costly
However, encapsulation is not always the best choice. It’s typically not recommended for materials that are already damaged or in high-traffic areas where they might face wear and tear.
Encapsulation vs. Removal
Choosing between asbestos encapsulation and removal depends on various factors such as:
- Cost: Encapsulation is often less expensive than removal
- Time: Encapsulation usually takes less time to complete
- Long-term management: Removal eliminates the asbestos, while encapsulation requires ongoing monitoring
- Building plans: If future renovations are likely, removal might be preferable
Each method has its advantages and drawbacks. The right choice depends on the specific situation, the condition of the asbestos-containing materials, and long-term plans for the building.
It’s important to note that both encapsulation and removal should only be carried out by certified professionals who can ensure the work is done safely and effectively.
What Are The Steps For Commercial Asbestos Encapsulation?
The process of commercial asbestos encapsulation involves several important stages:
- Inspection: Experts examine the asbestos-containing materials to assess their condition. They determine if encapsulation is a suitable option based on factors like material type, location, and state of repair.
- Surface Preparation: Before applying encapsulants, workers clean the area thoroughly. They remove dust and debris, and repair any damaged surfaces. This step ensures the encapsulant will adhere properly.
- Application of Encapsulating: Agents Technicians select appropriate sealants based on the specific materials and environment. They then apply the encapsulant carefully, making sure to cover all exposed asbestos-containing surfaces completely.
- Post-Encapsulation Monitoring: After application, inspectors check for proper coverage and adherence. They also set up a schedule for ongoing inspections to maintain the encapsulation’s effectiveness over time.
The initial asbestos inspection helps decide if encapsulation is the right approach. Proper surface preparation creates a stable base for the encapsulant. Careful application seals the asbestos-containing materials securely. Lastly, ongoing monitoring maintains the encapsulation’s integrity.
By following this process, businesses can effectively manage asbestos risks without full removal when appropriate. This method can offer a less disruptive and often more cost-effective solution in many cases.
How Do I Know If A Commercial Building Contains Asbestos?
The most reliable way to identify asbestos is through an inspection by a certified professional. These experts have the training and equipment to:
- Visually assess potential asbestos-containing materials
- Take samples safely for laboratory analysis
- Provide a detailed report on asbestos presence and condition
Asbestos was used in many building materials before its dangers were fully understood. Here’s a table of common materials and their typical usage periods:
Material | Years Used |
Pipe insulation | 1920s – 1970s |
Sprayed-on fireproofing | 1935 – 1970s |
Vinyl floor tiles | 1950s – 1980s |
Roofing felt | 1910s – 1980s |
Textured ceiling paint | 1945 – 1980s |
Signs of Possible Asbestos Presence
While not definitive, these signs might indicate asbestos:
- Building age (constructed before 1980)
- Fibrous or fluffy insulation materials
- Corrugated cement roofing
- Old floor tiles with a marbled pattern
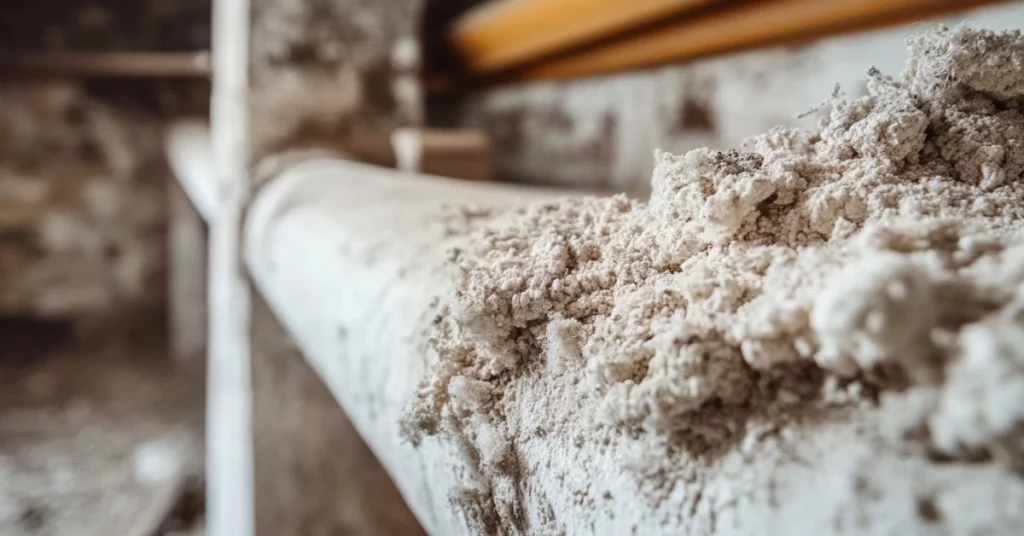
Asbestos is only dangerous when disturbed. If you suspect its presence, don’t attempt removal yourself. Contact a certified asbestos inspector to assess the situation safely.
By understanding these aspects of asbestos detection, building owners can take appropriate steps to manage any asbestos-related risks in their properties.
What Does Asbestos Look Like In Commercial Properties?
Asbestos can take many forms in commercial buildings. While visual identification alone isn’t reliable, knowing how asbestos-containing materials might appear can help property owners and managers recognize potential risks.
Insulation:
Asbestos insulation often has a fluffy, fibrous texture. It’s typically white or grayish and is commonly found around pipes, boilers, or in attics. The fibers may look like soft, woolly material.
Floor Tiles:
Asbestos-containing floor tiles are often 9×9 inches in size, especially in older installations. They frequently have a marbled or speckled pattern and come in various colors such as beige, gray, or brown. The tiles may become brittle or crack with age.
Ceiling Tiles:
These are usually square or rectangular. Asbestos-containing ceiling tiles may have a pinhole or textured surface. They’re often off-white or pale gray in color. Some may show signs of water damage or discoloration.
Roofing Materials:
Corrugated cement sheets used for roofing may contain asbestos. These are usually gray and can appear weathered or worn over time. They might have a rough, fibrous texture when damaged.
Spray-On Coatings:
These have a textured or popcorn-like appearance, often found on ceilings or walls. The color can be white, gray, or slightly yellowish. The surface may look uneven or bumpy.
It’s important to note that materials containing asbestos often look similar to asbestos-free alternatives. The only way to confirm asbestos presence is through professional testing. If you suspect a material might contain asbestos:
- Don’t touch or disturb it
- Treat it as if it contains asbestos until proven otherwise
- Consult a certified asbestos professional for proper identification
By being aware of these potential appearances, you can better recognize possible asbestos hazards in commercial properties. However, always rely on professional inspection for accurate identification and safe management of asbestos-containing materials.
How Much Does Commercial Asbestos Removal Cost?
Commercial asbestos removal cost varies widely based on several factors. Understanding these can help property owners and managers budget for this important safety measure.
Key Cost Factors:
- Project Size: Larger areas typically cost more to treat.
- Asbestos Amount: More asbestos means higher removal costs.
- Removal Complexity: Hard-to-reach areas or mixed materials increase expenses.
- Location: Labor and disposal costs differ by region.
- Type of Asbestos: Some forms are more challenging to remove.
Average Cost Ranges:
- Small projects (under 1,500 sq ft): $15,000 – $25,000
- Medium projects (1,500 – 3,000 sq ft): $25,000 – $50,000
- Large projects (over 3,000 sq ft): $50,000+
These figures are estimates. Actual costs can vary significantly.
Additional Expenses:
- Permits: $100 – $2,000
- Pre-removal testing: $400 – $900
- Post-removal testing: $400 – $900
- Containment systems: $500 – $5,000
Cost Breakdown Table:
Cost Factor | Percentage of Total Cost |
Labor | 60-70% |
Materials | 10-15% |
Disposal | 10-15% |
Testing | 5-10% |
Cutting corners on asbestos removal can lead to health risks and legal issues. Always work with certified professionals and get multiple quotes for accurate pricing.
Proper asbestos removal is an investment in safety and long-term property value. While costs can be significant, they’re often less than potential legal and health expenses from improper management.
How Much Time Does Commercial Asbestos Removal Take?
Commercial asbestos removal timelines vary based on several elements. Building size significantly influences duration – larger structures naturally take longer to process. The extent of asbestos contamination also impacts the timeline, with more widespread issues requiring additional time.
Project complexity affects duration too. Asbestos in hard-to-reach areas or mixed with other materials often extends the process. Regulatory requirements, including permits and inspections, can add extra days.
Team size influences timelines as well. More workers might speed up removal, but this approach often increases costs.
Here are some general timeframes:
Small projects, like a single room, typically take 4-9 days total. This includes 1-2 days for preparation, 2-5 days for removal, and 1-2 days for clearance testing.
Medium-sized projects involving multiple rooms or floors usually require 2-4 weeks. Preparation takes 3-5 days, removal lasts 1-3 weeks, and clearance testing needs 2-3 days.
Large projects covering entire buildings can span 6-16 weeks. Preparation might take 1-2 weeks, removal 1-3 months, and clearance testing about a week.
Project Timeline Chart:
Project Phase | Small Project | Medium Project | Large Project |
Preparation | 1-2 days | 3-5 days | 1-2 weeks |
Removal | 2-5 days | 1-3 weeks | 1-3 months |
Clearance Testing | 1-2 days | 2-3 days | 1 week |
Remember, these are estimates. Actual project durations can differ based on specific circumstances. Unexpected issues may extend timelines, while rush jobs might be possible at higher costs.
Proper planning helps minimize business disruptions. For accurate time estimates tailored to your situation, always consult certified asbestos removal specialists.
How Much Does Commercial Asbestos Encapsulation Cost?
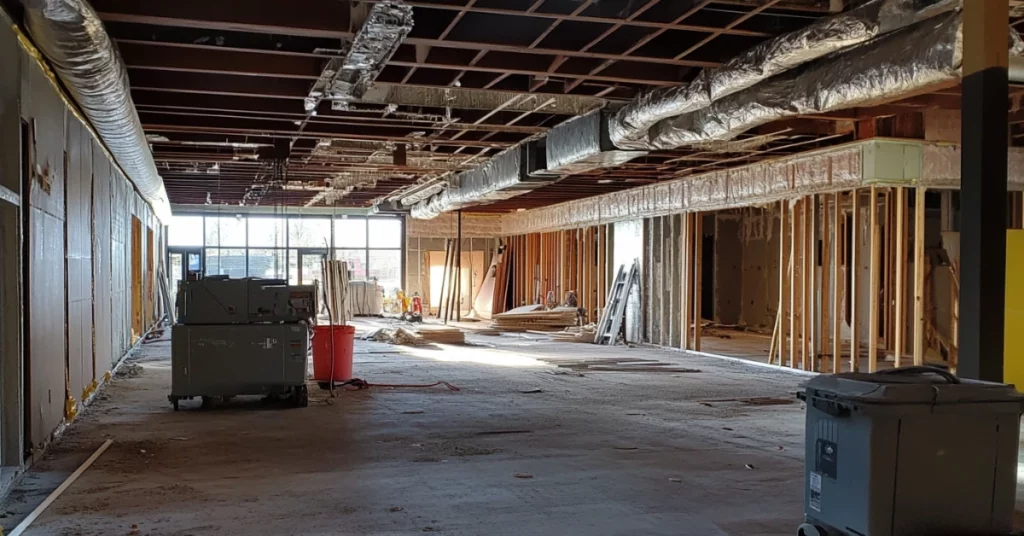
Commercial asbestos encapsulation costs vary based on several aspects of the project. The size of the area plays a significant role – larger spaces require more materials and labor, increasing overall expenses.
The type of encapsulant used also impacts pricing. Different materials come with varying costs, and some specialized encapsulants may be more expensive but offer better long-term protection.
Project complexity contributes to the final price. Encapsulating asbestos in hard-to-reach areas or on irregular surfaces often requires more time and effort, raising the cost.
Surface preparation is another consideration. If the asbestos-containing materials are damaged, they may need repair before encapsulation can begin, adding to the total expense.
Location affects pricing too, as labor rates differ by region.
Here are some average cost ranges:
- Small projects (under 1,000 sq ft): $2,000 – $5,000
- Medium projects (1,000 – 2,000 sq ft): $5,000 – $15,000
- Large projects (over 2,000 sq ft): $15,000+
Additional expenses may include inspection fees ($200 – $800) and air quality testing ($200 – $600).
When comparing encapsulation to removal, consider this cost breakdown:
Aspect | Encapsulation | Removal |
Initial Cost | $2 – $6 per sq ft | $10 – $20 per sq ft |
Duration | 1-7 days typically | 1-3 weeks typically |
Disruption | Minimal | Significant |
Long-term Cost | Ongoing monitoring | One-time expense |
Encapsulation often costs less initially but requires ongoing monitoring. Removal has higher upfront costs but eliminates future asbestos concerns.
Your choice should depend on your specific situation, budget, and long-term plans for the property. Always consult certified professionals for accurate, project-specific estimates to ensure you’re making an informed decision about managing asbestos in your commercial property.
How Much Time Does Commercial Asbestos Encapsulation Take?
Commercial asbestos encapsulation is an alternative to removal that involves coating asbestos-containing materials with a sealant. The time required for this process varies depending on several elements.
The size of the affected area significantly impacts the asbestos encapsulation timeline. Larger areas naturally require more time to treat. For instance, a small office space might take a day or two, while a large warehouse could require weeks.
The type of encapsulating material used also affects the duration. Some sealants dry faster than others, influencing the overall project time. Quick-drying products may shorten the process, but they might not be suitable for all situations.
The condition of the asbestos-containing materials is another factor. Damaged or friable asbestos may need additional preparation time before encapsulation can begin, extending the project duration.
Accessibility of the area plays a role too. Hard-to-reach spaces, such as crawl spaces or high ceilings, can slow down the process as workers need to take extra safety precautions.
Typical timeframes for commercial asbestos encapsulation are:
- Small-scale projects (under 100 square feet): 1-3 days
- Medium-scale projects (100-1000 square feet): 3-7 days
- Large-scale projects (over 1000 square feet): 1-4 weeks or more
Compared to asbestos removal, encapsulation often takes less time. Removal requires additional steps like complete isolation of the area, careful extraction of materials, and thorough cleaning. However, in some cases where the asbestos-containing materials are easily accessible and in good condition, removal might be quicker.
Here’s a breakdown of the encapsulation process and its approximate duration:
- Initial assessment and planning: 1-3 days
- Preparation of the area: 1-2 days
- Application of encapsulant: 1-5 days (depending on project size)
- Curing and drying time: 1-3 days
- Final inspection and clearance: 1 day
The time for asbestos encapsulation can vary widely based on project specifics. It’s best to consult with a professional asbestos abatement company for an accurate estimate tailored to your situation. They can assess the unique aspects of your project and provide a more precise timeline.
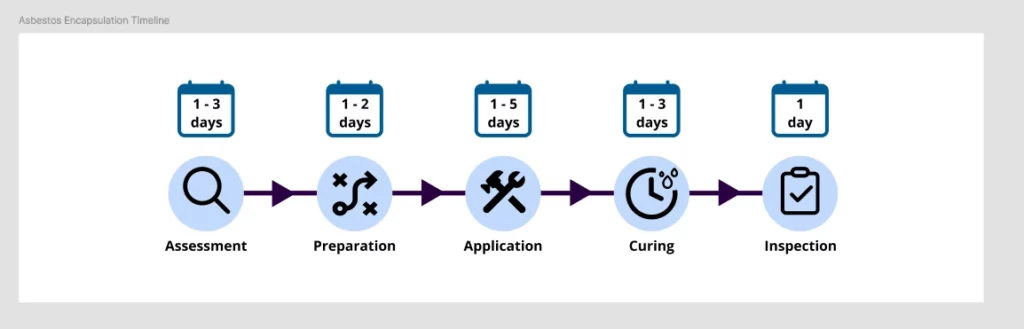
This timeline graphic visually represents the steps and approximate durations of the asbestos encapsulation process. It provides a quick overview of the project phases, helping readers understand the time investment required for each stage.
What Should I Do In An Asbestos Emergency?
An asbestos emergency occurs when asbestos-containing materials (ACMs) are unexpectedly disturbed, potentially releasing harmful fibers into the air. Quick and proper response is vital to minimize health risks and environmental contamination. This guide outlines the steps for an effective asbestos emergency response.
Immediate Safety Measures:
- Evacuate the area: Clear all personnel from the affected zone immediately. Use calm but firm communication to prevent panic.
- Isolate the affected zone: Seal off the area to prevent further spread of potential asbestos fibers. Use plastic sheeting and duct tape to cover doorways, windows, and vents.
- Turn off ventilation systems: Shut down HVAC systems to stop air circulation, which could spread asbestos fibers to other parts of the building.
Notification Process:
- Inform building management: Alert the property manager or building owner about the incident.
- Contact local health department: Notify your local health or environmental agency about the emergency. They can provide guidance on next steps and regulatory requirements.
- Notify employees or occupants: Inform all building occupants about the situation and the areas to avoid.
Engaging Professional Help:
- Call licensed asbestos professionals: Contact a certified asbestos abatement company for emergency asbestos removal. They have the expertise and equipment to handle the situation safely.
- Seek emergency services if needed: If there are injuries or if the situation poses immediate danger, call emergency services.
Documentation and Record-Keeping:
- Document the incident: Record details of the emergency, including time, location, extent of damage, and actions taken.
- Keep a log of all communications: Note down all calls made and instructions received from authorities and professionals.
Post-Emergency Actions:
- Facilitate air quality testing: Allow professionals to conduct air sampling to determine the extent of asbestos fiber release.
- Oversee cleanup and decontamination: Licensed professionals will perform thorough cleanup using specialized equipment and procedures.
- Review and update asbestos management plan: Use insights from the incident to improve your asbestos management strategies.
Prevention of Future Incidents:
- Conduct staff training: Educate employees about asbestos risks and proper emergency procedures.
- Schedule regular inspections: Implement routine checks of known asbestos-containing materials to prevent unexpected disturbances.
- Keep your asbestos register updated: Regularly review and update your record of asbestos locations in the building.
Only trained and licensed professionals should handle asbestos-containing materials directly. Your primary role is to ensure safety, notify the right people, and facilitate professional intervention.
Do Asbestos Removal Companies Offer Emergency Services?
Many asbestos removal companies offer emergency services to handle unexpected asbestos-related incidents. These services are designed to address situations where asbestos-containing materials (ACMs) have been unexpectedly disturbed or damaged, posing an immediate risk to building occupants.
Emergency asbestos removal services typically handle various situations, including:
- Accidental damage to ACMs during renovation or maintenance
- Natural disasters that compromise asbestos-containing structures
- Fire or water damage in buildings with known asbestos presence
- Unexpected discovery of asbestos during construction work
Response times for emergency asbestos services vary, but many companies aim to be on-site within 2-4 hours of receiving a call. Some offer 24/7 availability to ensure round-the-clock coverage for asbestos emergencies.
To contact emergency asbestos removal services:
- Search online for “emergency asbestos removal” in your area
- Check with your local environmental health department for recommended providers
- Have your building’s asbestos management plan handy, as it may list preferred contractors
When calling, be prepared to provide:
- Your location and contact information
- Nature of the emergency (e.g., type of damage, suspected asbestos material)
- Size of the affected area
- Whether the building is occupied
The emergency response process typically involves:
- Initial assessment: Professionals will evaluate the situation and potential risks
- Containment: The area will be isolated to prevent further spread of asbestos fibers
- Air monitoring: Testing may be conducted to assess airborne asbestos levels
- Removal or repair: Depending on the situation, the ACM may be removed or sealed
Swift action in asbestos emergencies is vital. Exposure to airborne asbestos fibers can lead to serious health issues, including lung cancer and mesothelioma. Quick response also helps comply with legal and regulatory requirements regarding asbestos management.
It’s important to note that emergency asbestos removal often comes at a premium cost compared to planned removal. However, many insurance policies cover emergency asbestos services, especially if the incident was caused by an insured event like fire or storm damage.
Emergency Asbestos Removal Services
Asbestos removal companies typically offer the following emergency services:
- 24/7 Emergency Response: Round-the-clock availability for urgent situations
- Rapid On-Site Assessment: Quick evaluation of the asbestos risk and extent of the problem
- Air Monitoring: Testing air quality to determine the level of asbestos fiber release
- Containment: Sealing off affected areas to prevent further spread of asbestos fibers
- Emergency Removal: Safe extraction of damaged asbestos-containing materials
- Encapsulation: Sealing exposed asbestos if immediate removal is not feasible
- Decontamination: Thorough cleaning of the affected area and surrounding spaces
- Waste Disposal: Proper handling and disposal of asbestos waste
- Post-Incident Air Clearance Testing: Ensuring the area is safe for reoccupation
- Documentation: Providing necessary reports for insurance and regulatory compliance
- Emergency Repair: Temporary fixes to prevent further asbestos disturbance
- Coordination with Other Emergency Services: Working alongside fire departments, etc., in disaster scenarios
Remember: Always prioritize safety and only work with licensed, experienced asbestos professionals.
Many asbestos removal companies do offer emergency services, providing swift and comprehensive responses to unexpected asbestos incidents. These services are designed to quickly contain the risk, protect building occupants, and ensure proper handling of the hazardous material.
While emergency removal can be costly, the potential health risks and legal implications of delayed action far outweigh the financial considerations.
To be best prepared for potential asbestos emergencies:
- Maintain an up-to-date asbestos management plan
- Keep contact information for emergency asbestos services readily available
- Ensure key personnel are trained in emergency response procedures
- Conduct regular inspections to catch potential issues before they become emergencies
Remember, when it comes to asbestos, it’s always better to be overprepared. Quick access to emergency asbestos removal services can make a significant difference in minimizing health risks and property damage in the event of an unexpected incident.
How Quickly Can Asbestos Be Safely Removed In An Emergency?
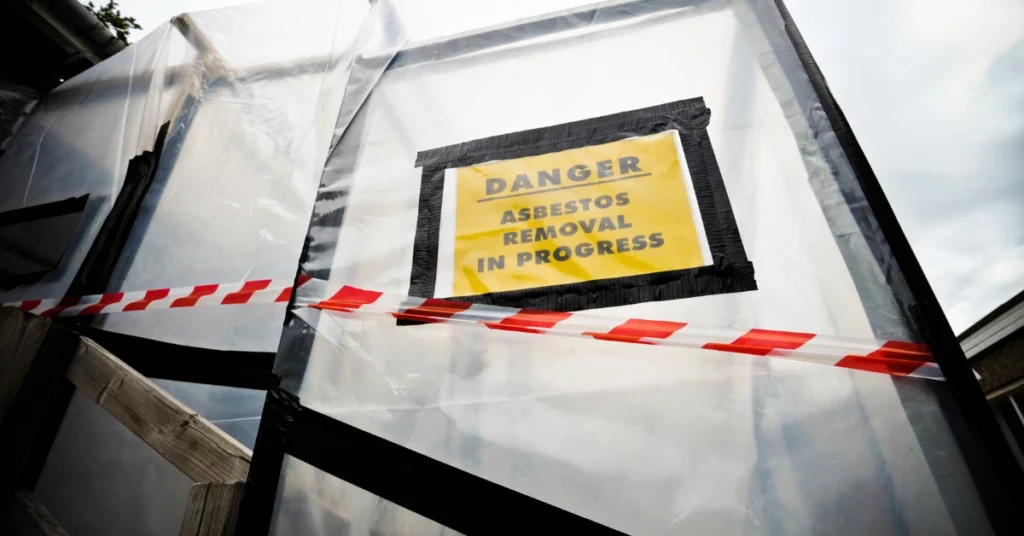
Emergency asbestos removal requires swift action to protect people from exposure to harmful fibers. The asbestos emergency removal timeline can vary based on several elements, but professional teams aim for the fastest possible response while maintaining safety standards.
The speed of removal depends on:
- The severity of the situation
- The size of the affected area
- The type of asbestos-containing materials
- The accessibility of the site
In many cases, asbestos removal companies can dispatch teams to assess the situation within hours of receiving an emergency call. The initial evaluation typically takes 1-2 hours, during which experts determine the extent of the problem and plan the removal strategy.
Containment measures are the first step in the rapid asbestos removal process. Experienced teams can set up containment areas in as little as 2-4 hours for smaller spaces, while larger areas might require 6-8 hours or more.
The actual removal process duration varies widely. For small-scale emergencies, such as a damaged asbestos ceiling tile in a single room, removal might be completed in 4-6 hours. Larger commercial incidents could take several days to address fully.
Case studies highlight the effectiveness of emergency asbestos removal services:
- In a residential emergency where a storm damaged asbestos siding on a house, a removal team arrived within 2 hours, set up containment in 3 hours, and completed the removal process in 8 hours.
- A large commercial building experienced significant damage to asbestos insulation due to a fire. The removal team was on-site within 90 minutes, established containment zones over 12 hours, and completed the removal over a 72-hour period.
Safety remains paramount in rapid asbestos removal. Teams use specialized equipment for quick containment and efficient removal methods to reduce time without compromising protection. Workers wear appropriate personal protective equipment and follow strict protocols to prevent fiber release.
After removal, air quality testing and clearance procedures are conducted to ensure the area is safe for reoccupation. These final steps typically take 24-48 hours, depending on the size of the affected area.
While speed is important in emergencies, proper safety measures must be maintained throughout the process. Professional asbestos removal services strike a balance between rapid response and thorough, safe removal to protect both workers and building occupants.
Why Hire Certified Asbestos Removal Professionals for Commercial Buildings?
Safety is the primary reason to hire certified asbestos contractors. They understand the proper handling and containment techniques required to prevent the release of harmful asbestos fibers into the air. These professionals use specialized equipment and follow strict protocols to protect themselves, building occupants, and the environment during the removal process.
Regulatory compliance is another significant advantage of working with asbestos removal professionals. They stay updated on local, state, and federal regulations governing asbestos removal and disposal. This knowledge ensures that your commercial building remains compliant with all relevant laws, reducing the risk of fines or legal issues.
Hiring certified contractors also provides legal liability protection. These professionals carry appropriate insurance coverage, which can shield building owners from potential lawsuits related to asbestos exposure. In contrast, using uncertified contractors can leave you vulnerable to legal and financial consequences if something goes wrong during the removal process.
The expertise and experience of certified asbestos removal professionals are invaluable. Their specialized training enables them to identify different types of asbestos-containing materials and choose the most appropriate removal methods. This expertise leads to more efficient and thorough asbestos removal, reducing the likelihood of future issues.
Using uncertified contractors comes with significant risks. They may employ improper removal methods, potentially releasing asbestos fibers into the air and creating a health hazard. This can lead to expensive cleanup efforts, potential lawsuits, and damage to your business’s reputation.
Benefits of hiring certified asbestos contractors for commercial buildings:
- Ensure proper asbestos handling and disposal
- Comply with all relevant regulations
- Reduce legal liability
- Protect the health of building occupants and workers
- Receive professional documentation of the removal process
- Benefit from efficient and thorough removal techniques
- Gain peace of mind knowing the job is done correctly
In the long run, hiring certified asbestos removal professionals is cost-effective. By ensuring thorough removal and proper disposal, you prevent future asbestos-related issues and avoid the need for repeated removal attempts. This approach saves money and protects your commercial property’s value over time.
Certified asbestos contractors bring a level of expertise and professionalism that is indispensable when dealing with such a dangerous material. Their training, knowledge, and commitment to safety make them the clear choice for asbestos removal in commercial buildings.
How to Choose the Right Asbestos Removal Contractor?
Choosing an asbestos contractor for your commercial project is a task that can ensure a safe, efficient, and compliant removal process. Here’s how to evaluate and select the best asbestos removal companies for your needs.
Essential Qualifications and Certifications: Verify that potential contractors hold all required licenses and certifications for asbestos removal in your area. Ask for proof of liability insurance and workers’ compensation coverage. These documents protect you and the contractor in case of accidents or issues during the removal process.
Experience and Expertise: Look for contractors with substantial experience, particularly in commercial asbestos removal. Ask about their years in business and the types of projects they’ve handled. Contractors who specialize in commercial buildings often have a better understanding of the unique challenges these projects present.
Reputation and Track Record: Research the contractor’s reputation by requesting client references and reading online reviews. Check their standing with professional associations and the Better Business Bureau. A strong track record of successful projects and satisfied clients is a good indicator of reliability.
Evaluation of Services: Assess the range of services each contractor offers. The best asbestos removal companies typically provide comprehensive services, including inspection, removal, and post-removal testing. Inquire about their equipment and techniques to ensure they use up-to-date methods for efficient and safe removal.
Cost Considerations: Request detailed cost estimates from multiple contractors. Make sure you understand what’s included in each estimate. The lowest bid isn’t always the best choice – consider the overall value, including the contractor’s reputation and the quality of their work.
Safety Protocols and Compliance: Ask about the contractor’s safety protocols and how they ensure compliance with regulations. Inquire about their employee training programs and certification processes. A commitment to safety is paramount in asbestos removal.
Communication and Project Management: Evaluate the contractor’s communication style and responsiveness. Clear, open communication is key to a successful project. Ask about their project management approach, including how they handle timelines, reporting, and any unexpected issues that may arise.
Checklist for Choosing an Asbestos Contractor:
- Verify licenses and certifications
- Check insurance coverage
- Assess experience in commercial projects
- Review client testimonials and references
- Evaluate range of services offered
- Compare detailed cost estimates
- Inquire about safety protocols and employee training
- Assess communication and project management style
To help you compare potential contractors, use a comparison table like this:
Criteria | Contractor A | Contractor B | Contractor C |
Years of experience | |||
Certifications | |||
Insurance coverage | |||
Commercial expertise | |||
Client reviews | |||
Services offered | |||
Cost estimate | |||
Safety record | |||
Communication |
By evaluating potential contractors using these criteria, you can make an informed decision and select a qualified, reliable asbestos removal professional for your commercial project. Remember, the right contractor not only ensures safety and compliance but also provides peace of mind throughout the removal process.
What Happens After Asbestos Is Removed From Commercial Properties?
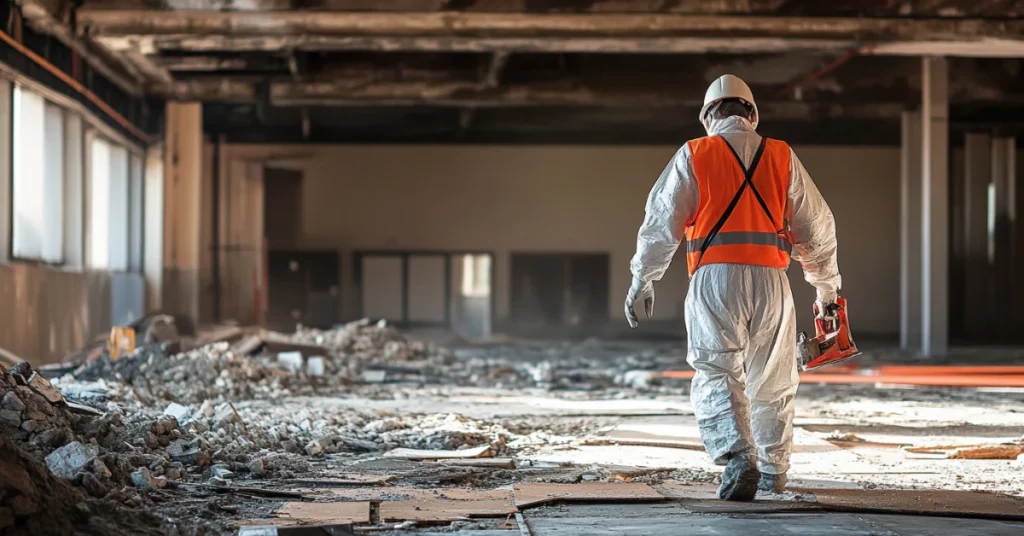
After asbestos removal from a commercial property, several important steps ensure the area is safe for reoccupation. These post-removal procedures are designed to verify that all asbestos has been properly removed and that no residual fibers remain in the air or on surfaces.
Site Cleanup: The first step after asbestos removal is a thorough site cleanup. This involves:
- Removing containment structures such as plastic sheeting and barriers
- Properly disposing of all contaminated materials, including protective equipment
- Cleaning all surfaces in the removal area using specialized techniques like HEPA vacuuming
This cleanup process aims to remove any remaining asbestos fibers and prepare the area for testing.
Air Quality Testing: Air quality testing is a critical component of post-removal procedures. It involves collecting air samples to measure the concentration of asbestos fibers. Technicians use specialized equipment to capture air samples, which are then analyzed in a laboratory. The results must meet specific standards set by regulatory agencies to ensure the area is safe.
Visual Inspections: Certified inspectors conduct thorough visual examinations of the removal areas. They look for any signs of remaining asbestos-containing materials or residual contamination. This step helps identify any spots that may have been missed during the removal process.
Final Clearance Testing: Final clearance testing is a comprehensive process that combines air testing and visual inspection. This step confirms that the asbestos removal was successful and that the area is safe for reoccupation. To pass clearance, the area must meet strict criteria for air quality and be free of visible asbestos-containing materials.
Documentation and Reporting: Throughout the post-removal process, detailed records are kept of all activities, test results, and inspections. These documents are compiled into a final report, which is provided to the property owner. This documentation is important for legal compliance and future reference.
Reoccupation Preparations: Once the area passes final clearance, preparations for reoccupation can begin. This may involve:
- Removing any remaining equipment or barriers
- Restoring any systems or structures that were affected by the removal process
- Conducting a final walkthrough with the property owner
Long-term Management: After the immediate post-removal procedures, it’s important to develop a long-term asbestos management plan. This plan outlines strategies for monitoring any remaining asbestos-containing materials in the building and procedures for addressing future asbestos-related issues.
These post-removal procedures are essential for ensuring that commercial properties are safe after asbestos removal. They provide peace of mind to property owners and occupants, confirming that the asbestos threat has been effectively addressed.
Why Is Post-Removal Air Quality Testing Important For Commercial Properties?
Post-removal air quality testing is a crucial step in the asbestos abatement process for commercial properties. This testing ensures that the air is free from asbestos fibers after removal, providing assurance that the space is safe for occupancy.
Ensuring Complete Asbestos Removal: Asbestos air testing after removal helps detect any residual fibers that may have been missed during the abatement process. Even small amounts of asbestos can pose health risks, making thorough testing essential. This verification confirms the effectiveness of the removal process and identifies any areas that may need additional attention.
Health and Safety Implications: The primary goal of post-removal air quality testing is to protect the health and safety of building occupants and workers. Asbestos fibers, when airborne, can be inhaled and cause serious health problems. By confirming that the air is clean, property owners can confidently allow people to return to the space without risking exposure.
Air Testing Process: Post-removal air quality assessments typically involve two main methods:
- Phase Contrast Microscopy (PCM): A quick and cost-effective method that counts all fibers in a sample.
- Transmission Electron Microscopy (TEM): A more precise method that specifically identifies asbestos fibers.
Technicians collect air samples from various locations within the abated area. These samples are then analyzed in a laboratory to determine the concentration of fibers present.
Interpreting Air Quality Test Results: Test results are typically expressed in fibers per cubic centimeter (f/cc) of air. The acceptable level for reoccupancy is usually less than 0.01 f/cc for PCM tests or 70 structures per square millimeter for TEM tests. Understanding these results is key to determining whether additional cleaning or removal is needed.
Legal and Regulatory Compliance: Post-removal air quality testing helps commercial properties meet industry standards and regulatory requirements. The documentation provided by these tests offers important liability protection, demonstrating due diligence in ensuring a safe environment.
Impact on Building Reoccupation: Clearance from air quality testing is often required before a building can be legally reoccupied. This clearance provides confidence to property owners, occupants, and regulatory bodies that the space is safe for normal use.
Comparison of Pre- and Post-Removal Air Quality Levels:
Aspect | Pre-Removal | Post-Removal (Goal) |
Asbestos fiber count | Variable, often elevated | <0.01 f/cc (PCM method) |
Air safety status | Potentially hazardous | Safe for occupancy |
Regulatory compliance | Non-compliant | Compliant |
Occupant health risk | High | Minimal to none |
Long-term Benefits: Thorough post-removal air testing provides long-term benefits for commercial properties. It establishes a baseline for future air quality monitoring and contributes to a comprehensive asbestos management plan. This proactive approach can prevent future asbestos-related issues and associated costs.
Post-removal air quality testing is more than a regulatory requirement—it’s a critical step in ensuring the health and safety of everyone who enters the commercial property.
By verifying that asbestos fibers have been effectively removed, this testing provides peace of mind and legal protection for property owners and occupants alike. It marks the successful completion of the asbestos abatement process and paves the way for safe, continued use of the commercial space.
Why Is Post-Encapsulation Air Quality Testing Important For Commercial Properties?
Post-encapsulation air quality testing is a vital step in managing asbestos in commercial properties. Encapsulation involves coating asbestos-containing materials with a sealant to prevent fiber release. Air testing after encapsulation verifies that this process has been effective and that the environment is safe for occupants.
Verifying Encapsulation Effectiveness: The primary purpose of air testing after encapsulation is to confirm that the asbestos-containing materials have been properly sealed. This testing can detect any immediate failures in the encapsulation process, such as areas that may have been missed or inadequately covered. By identifying these issues early, property owners can address them promptly, preventing potential asbestos exposure.
Establishing a Safety Baseline: Post-encapsulation safety checks create a reference point for future monitoring. This baseline helps property managers track the long-term effectiveness of the encapsulation and detect any changes that might indicate deterioration over time. It also provides immediate confirmation that the air is safe for occupants to return to the space.
Regulatory Compliance: Many jurisdictions require air quality testing after asbestos encapsulation as part of their regulatory framework. This testing provides documentation that the encapsulation was performed correctly and that the property is in compliance with health and safety standards. Such documentation is often required for legal and insurance purposes.
Testing Process: The air testing after encapsulation typically involves the following steps:
- Collecting air samples from various locations in the encapsulated area
- Using specialized equipment to capture airborne particles
- Sending samples to an accredited laboratory for analysis
- Comparing results to established safety standards
Analysis and interpretation of results focus on the concentration of asbestos fibers in the air. The commonly accepted standard for safety is less than 0.01 fibers per cubic centimeter of air (f/cc) when using phase contrast microscopy (PCM) for analysis.
Importance for Commercial Properties: For commercial properties, post-encapsulation air quality testing is particularly important. It helps protect employees, customers, and visitors from potential asbestos exposure. This testing also maintains the property’s value and reputation by demonstrating a commitment to safety and compliance.
Long-term Monitoring: While initial post-encapsulation testing is crucial, it’s also important to establish a schedule for ongoing monitoring. This helps ensure the continued effectiveness of the encapsulation over time. Regular testing should be integrated into the property’s overall asbestos management plan.
Post-encapsulation air quality testing is a critical step in ensuring the safety of commercial properties after asbestos management procedures. It provides verification of the encapsulation’s effectiveness, establishes a safety baseline, ensures regulatory compliance, and contributes to long-term asbestos management strategies. By conducting these tests, property owners demonstrate their commitment to maintaining a safe environment for all building occupants.